3 Ways Spreadsheets are Costing Your Construction Projects Time and Money
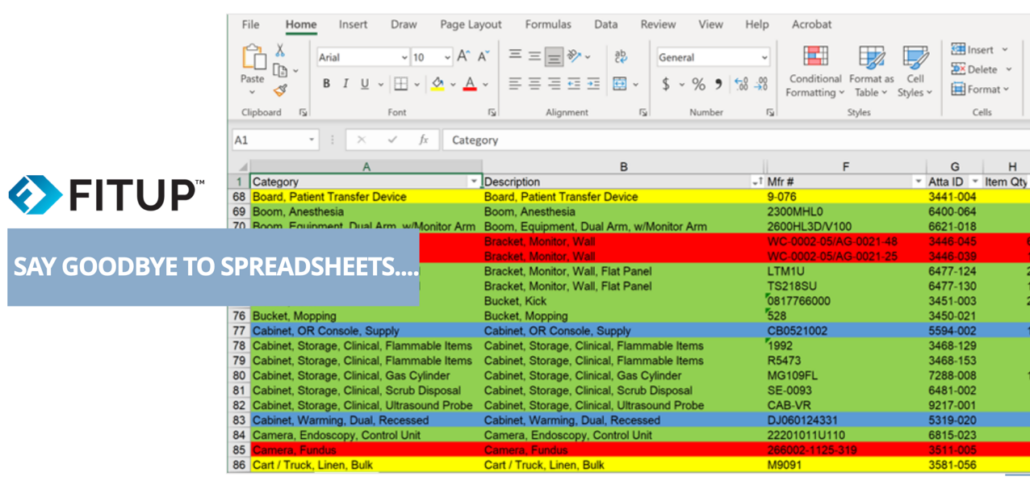
Before coming to FreightTrain for help, our customers were using excel spreadsheets to manage equipment logistics during the activation of their hospital construction projects. Your business is probably no different – relying on multiple spreadsheets and spreadsheet templates to manage this critical component of your healthcare construction projects.
Spreadsheets have their place in business, but that place is not in activating a building.
Here are 3 ways spreadsheets are creating waste for your construction project –
1) Wasted Time
How much time is each person involved in the activation of your construction projects spending inside spreadsheets?
You might be surprised by how high that number is for some of the people on your team. We often hear people are spending upwards of 50% of their time at work just trying to find the right spreadsheet, update it, send out the updated version to everyone involved, pull data from one to another, etc.
For example, several of our customers have told us they spent several hours each week compiling data from multiple spreadsheets to have a report they could give to the hospital leadership team. If you have two full-time project managers spending 8 hours a week each on generating reports from spreadsheets – that’s costing your business more than $1,000 every week, to create a report.
Close to 75% of contractors reported longer than expected project delays in 2022.
AGC 2022 Construction Hiring and Business Outlook Report
When your team’s time isn’t being used effectively, this is also a direct cause of project delays – adding further costs to your business.
FreightTrain’s FitUp automates reporting and delivers the latest reports in real-time. This means leadership always gets the most up-to-date status on the project, and project teams aren’t wasting up to a full workday double-handling project data to create reports. This ensures our customers’ projects launch on time.
2) Inaccurate Data
For large projects like a hospital facility, there are typically many spreadsheets and multiple teams of people who are transferring data across spreadsheets throughout the project. This leads to spreadsheets that are riddled with outdated and inaccurate information.
One recent report showed that over 86% of spreadsheets contain errors – and that a single error can cause up to 10% of that construction project’s value to be destroyed.
With our industry’s tight financial constraints, can any business afford to risk 10% of their next project’s value over a single spreadsheet error?
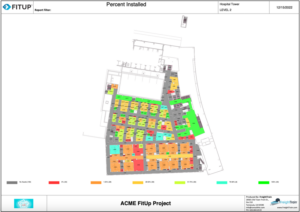
FitUp provides tools to verify data as it is entered into the database while dramatically reducing the errors caused when people are manually copying and pasting data from one spreadsheet to another. With more accurate data, our customers have fewer issues during their projects and can respond faster to issues as they arise.
3) Inhibits Collaboration
The activation of a hospital project involves numerous groups from multiple companies that all need to access and share information throughout the project. The inherent limitations of collaborating with spreadsheets often lead to frustration and difficulties across project teams when trying to track and report on key project KPIs over a construction project.
Creating and tracking a single issue that impacts multiple teams, such as having a piece of equipment ordered, delivered to the warehouse, sent onsite for installation, and then inspected, can rely on 10 or more spreadsheets that reside in different locations and are managed by different people. The typical hospital construction project will log and track over 5,000 issues – this isn’t feasible to manage in spreadsheets.
FitUp makes it easy for everyone involved to collaborate and maintain a single source of truth. Issues can be assigned to contractors within FitUp and tracked from the moment they were reported through resolution. Our platform streamlines project communications that used to be managed across multiple emails with multiple spreadsheet versions to track.
Consider eliminating spreadsheets from your project activation workflows as a new year’s resolution. Schedule a demo of FitUp today!