Don’t Allow Supply Chain Issues to Delay Your Project
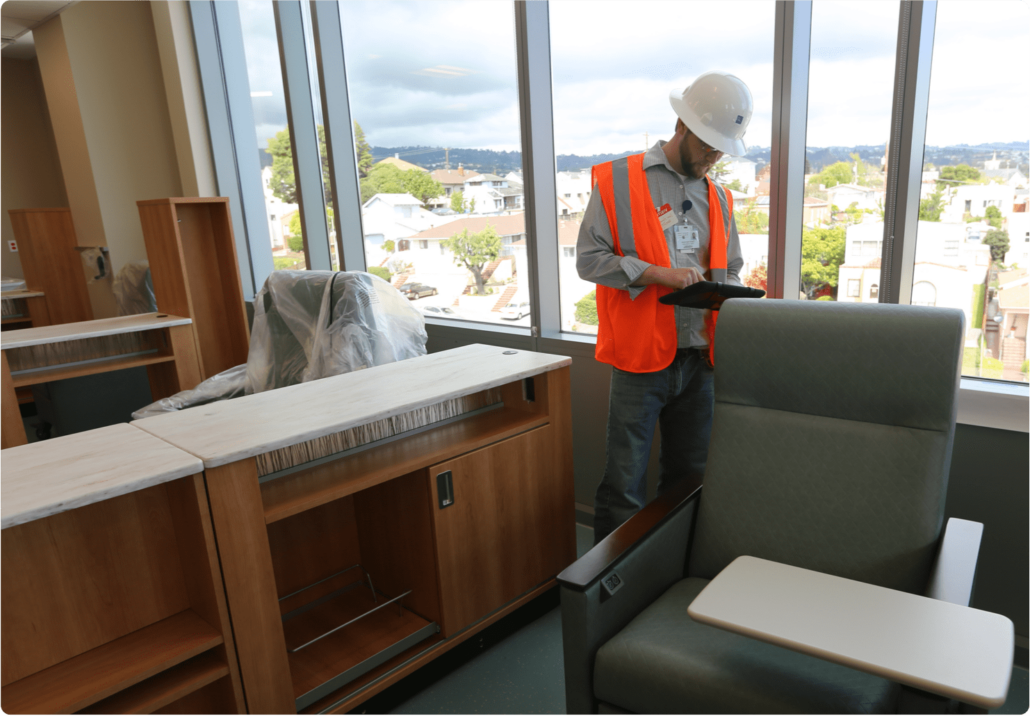
The last two years have been incredibly stressful for the healthcare industry and the many incredible people working in the field. In addition to the stress of treating an influx of patients caused by the COVID-19 pandemic, these organizations faced immense challenges in the supply chain. The issues with the supply chain are having a significant impact on organizations that are building and activating new facilities. Healthcare facilities are now facing delays upwards of five months for equipment to be delivered (Aeppel). These delays negatively impact the schedule for new projects and make it more challenging to provide patient care for all those in need.
Compounding the problem is that project teams in the field often have limited visibility to the status of the medical equipment, furniture, and IT devices that must be delivered and installed to open a new facility on time. Information about the status of these products often resides in spreadsheets exported from planning tools, ERP systems, and so forth. FitUp is a technology solution that allows healthcare organizations to track the ordering, shipment, and delivery of equipment, furniture, & IT. With FitUp, healthcare facilities can track, in real-time, on interactive dashboards what equipment has been purchased, shipped to the warehouse or the site, installed, tested, etc.
FitUp ensures that your project is successful and delivered on time. For more information, check out our website, https://www.usefitup.com/fitup/.
Best,
Aeppel, Timothy. “COVID Creates Shortages of an Array of U.S. Medical Supplies.” Reuters, 20 Sept. 2021, 11:23 a.m., https://docs.google.com/document/d/1rQTHnbHcOp92VSlnturN7g27WROsWwqBPbqiiOg7KYM/edit.